Automation and Robotics
We are leaders in automation and robotics applied to industrial processes. We optimise your processes to boost productivity and safety. Discover innovative solutions that transform efficiency into production. Join the automation vanguard for a more efficient and profitable industrial future.
We offer engineering services to optimise our clients' production processes. We analyse the specific needs of each company, the design and implementation of automated systems, as well as their programming and start-up. These automated solutions may include the use of industrial robots, control and monitoring systems, integration of sensors and actuators, among others.
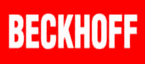
We are a Beckhoff Solution Provider
Solution providers in the industrial sector have extensive knowledge of PC-based control technology thanks to continuous exchange and further training.
This extensive knowledge enables the implementation of optimal, customer-specific solutions in the industrial environm.
Successful cases
Automation of unloading of components
In this application, we integrate three work points, centring the unloading at a single operator station. We automate the processes of the three work stations by means of robots and unify the unloading by using straight and curved conveyor belts. The improvements obtained:
-Installation of new safety enclosures in accordance with the requirements of the CE Directive.
-Safety management by a safety PLC
-Saving of two operators per shift
-Ergonomic improvement of operations
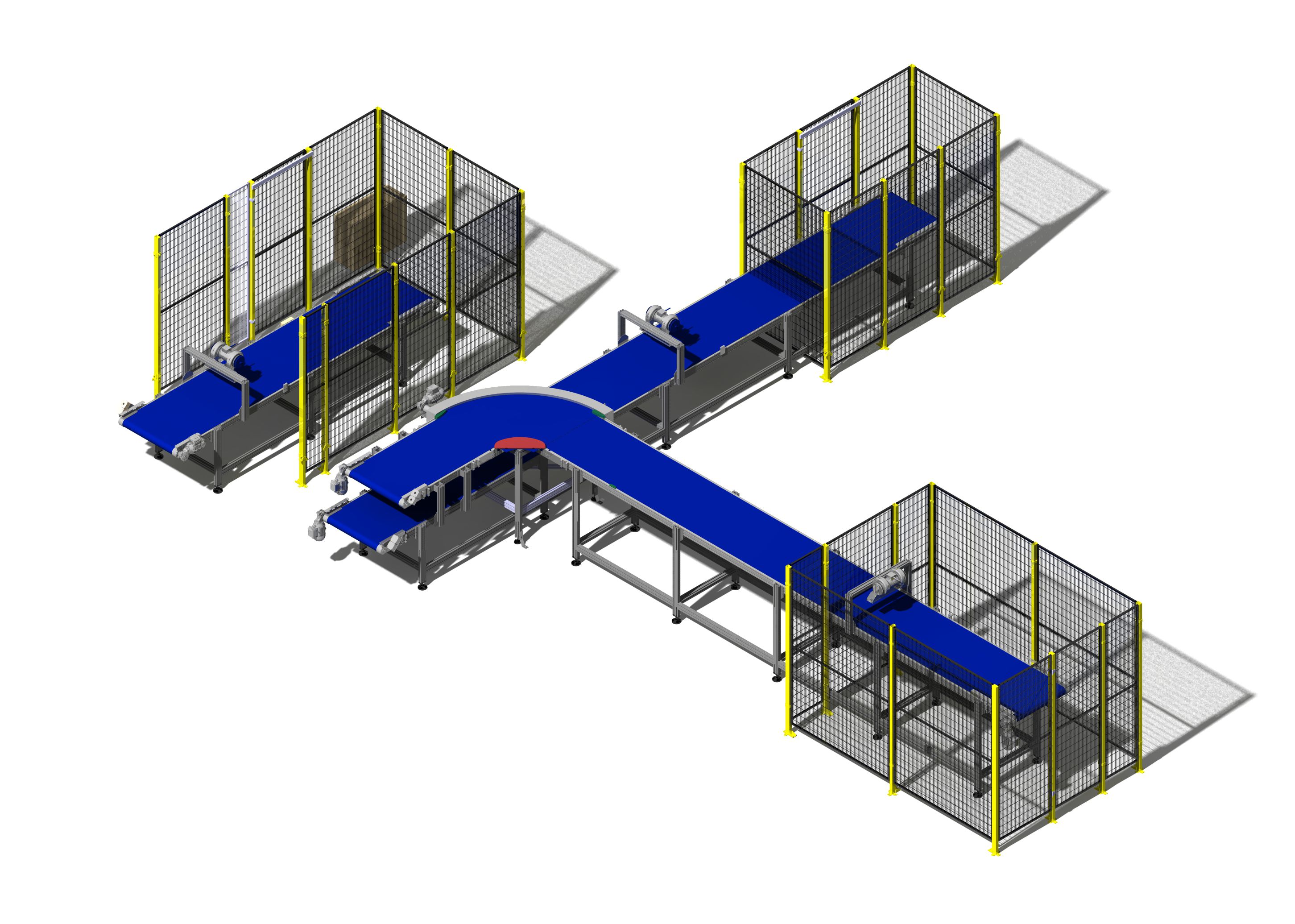
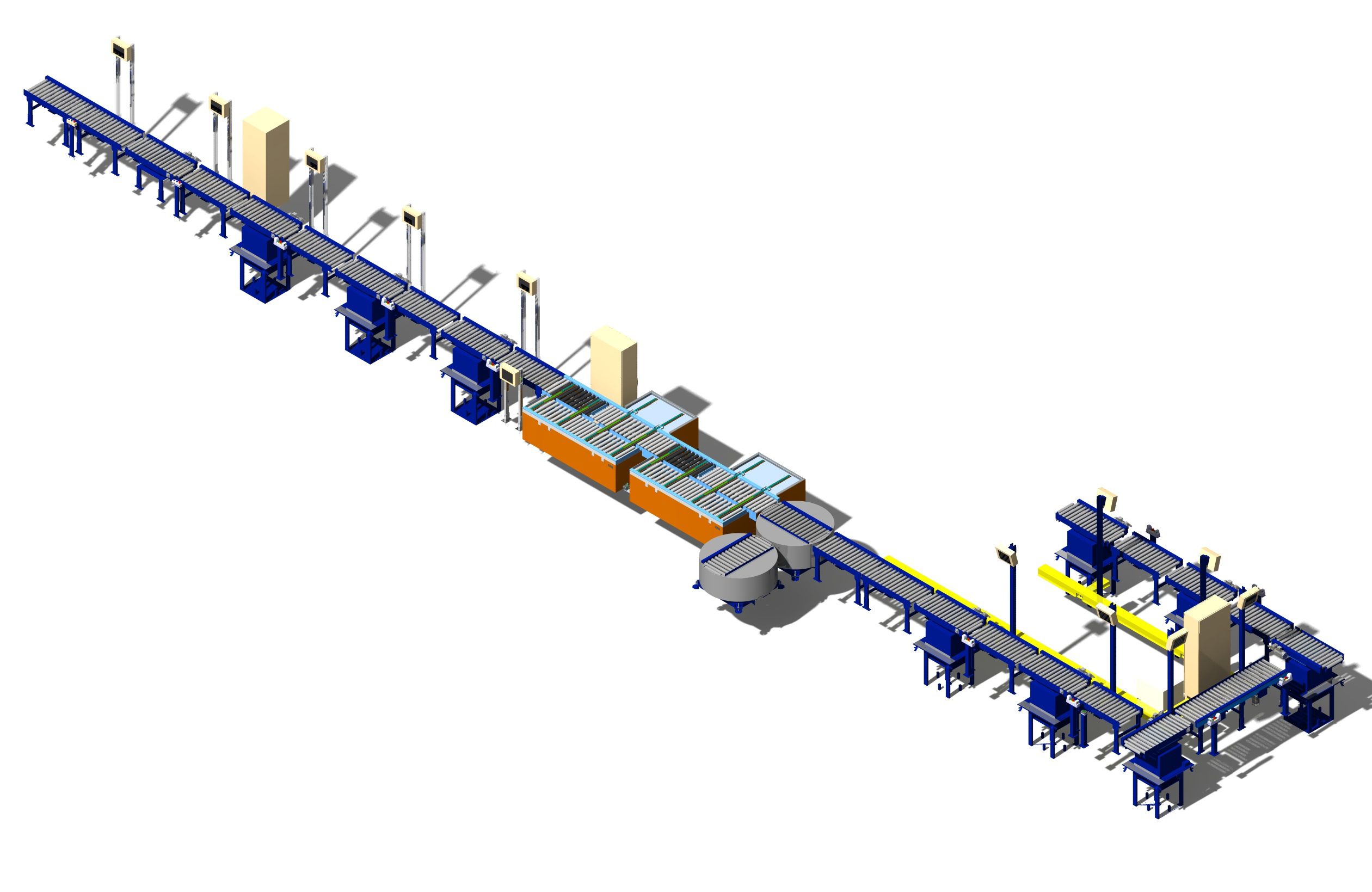
Automated production line
We manufacture and integrate a 50-metre automatic line with motorised roller conveyors, combining different conveyor models (with elevation, turning, bidirectional,...). In this line we combine different types of workstations and integrate machines from other manufacturers.
We carry out a completely turnkey project, from the conceptual design according to the premises of our clients, through the manufacture of all the mechanical elements, and finally programming and fine-tuning of the entire line.
The improvements achieved:
-Automatic product flow between functional areas
-Increased capacity and productivity rates
-Optimising the processing of workflows
-Tracking of each workstation through a customised traceability system.
-Fully scalable to accommodate future operational growth
-Optimal improvement of ergonomics thanks to our V6 motorised roller conveyors with 360° rotation and automatic elevation.
Automatic hydraulic press station
In this project the main objective was to improve the safety of the operator, it is a 10Tn hydraulic pressing process. To improve safety we installed an enclosure (in accordance with the CE Directive) and we carried out the loading and unloading operations of the press by means of a robot. By avoiding danger, we avoid accidents.Apart from the significant increase in safety, we obtained:
-Savings of 0.5 shift operator
-Repeatability of the process
-Reduction of "scrap"
-Productivity rates increase
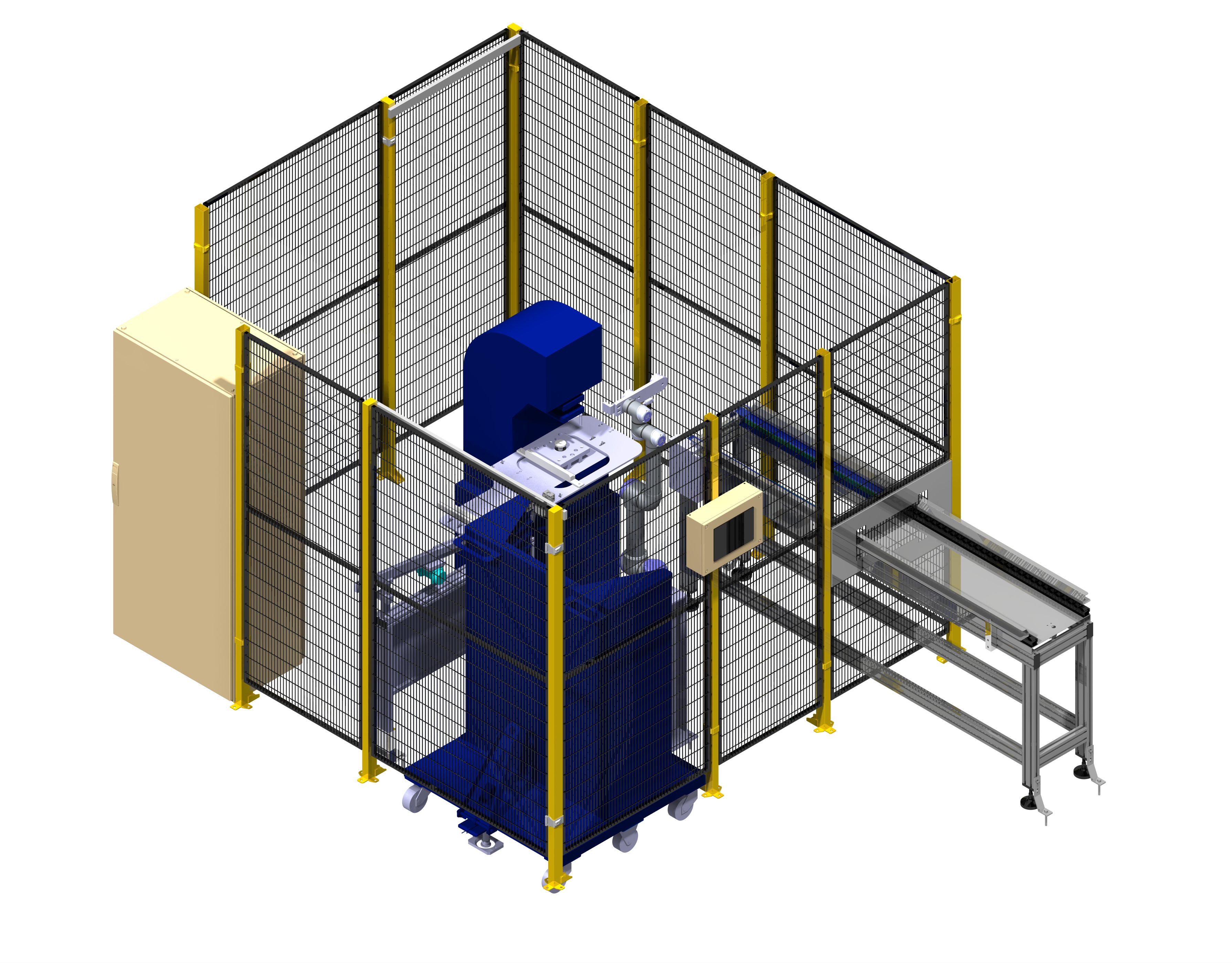
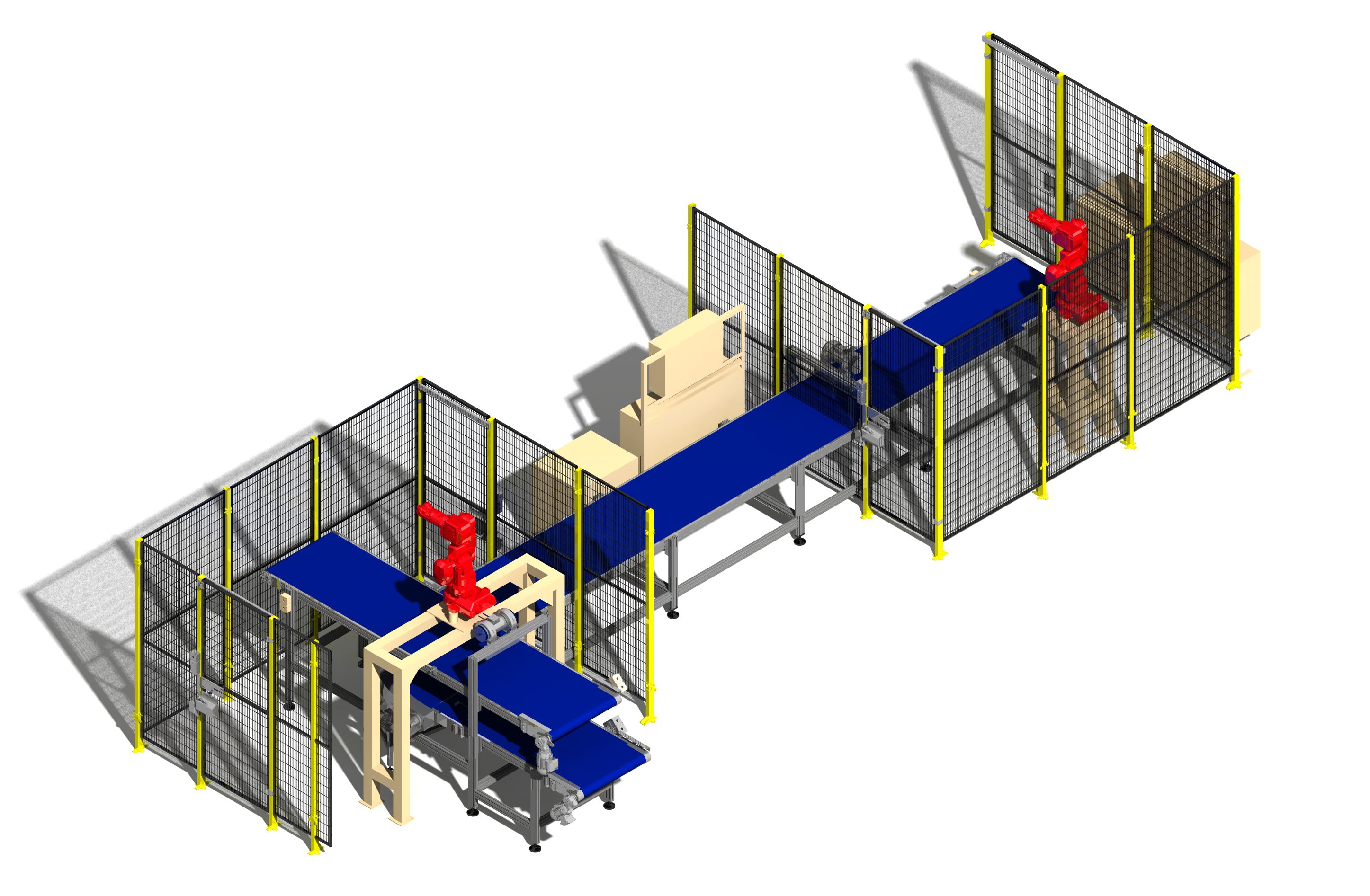
Automation of the flaming process
In this application we integrate two work points, centring the unloading at a single operator station. We automate the processes of the two workstations, moving on to perform a highly dangerous task such as flaming by robots and finally we unify the unloading by using straight and curved conveyor belts.
The most significant improvement was to perform the flaming operation by robot, removing the exposure of the operator to this hazard. Apart from this:
-Installation of new safety enclosures in accordance with the requirements of the CE Directive
-Safety management by a safety PLC
-Saving of one operator per shift
-Ergonomic improvement of operations